用Ⅱ类超晶格材料制备的红外探测器具有暗电流低、响应波段易于调控、均匀性易于控制等突出优点,为下一代红外探测器的发展提供了新方向。双色Ⅱ类超晶格红外探测器可比单色探测器得到更多的信息,具有更广泛的应用前景。现有双色探测器的器件成型路线分为单铟柱技术路线与双铟柱技术路线。其中,单铟柱技术路线的工艺步骤相对简单,易于实现。但单铟柱结构刻蚀过程中通常需要刻蚀较深的台面,这对现有的干法刻蚀工艺提出了更高的要求。采用双色单铟柱结构的Ⅱ类超晶格红外探测器件在台面成型过程中加工难度大且易于产生损伤,影响器件的性能。
据麦姆斯咨询报道,近期,华北光电技术研究所科研团队在《红外》期刊上发表了以“低损伤、高深宽比Ⅱ类超晶格材料的台面刻蚀技术研究”为主题的文章。该文章第一作者和通讯作者为李景峰,主要从事红外探测器设计及制备工艺开发的研究工作。
本文针对此问题进行了低损伤、高深宽比Ⅱ类超晶格材料的台面刻蚀技术研究。首先建立一种损伤评判机制,判断现有工艺刻蚀后材料是否发生反型。然后通过优化光刻胶厚度、变功率分步刻蚀的方式,实现低损伤、高深宽比Ⅱ类超晶格材料的台面刻蚀,同时有效解决单次刻蚀深台面时易堆积生成物以及侧壁过于陡峭等工艺问题。
实验过程
刻蚀Ⅱ类超晶格台面时,将正性光刻胶用作掩膜。对Ⅱ类超晶格材料进行干法刻蚀。刻蚀采用感应耦合等离子体(ICP)刻蚀机。刻蚀时BCl₃气体为刻蚀气体,Ar气体为惰性气体。Ar气既可保证工艺安全进行,又可通过调节其气量来控制反应速率。由于实现双色探测的技术路线采用单铟柱器件结构,所以进行一次台面刻蚀成型。采用分步刻蚀的方案实现深台面的刻蚀。台面中心间距为20 μm,设计台面宽度为15 μm,槽宽为5 μm。在台面成型且经过表面处理后,继续钝化、光刻电极孔、刻蚀电极孔、光刻电极和蒸镀电极,完成器件制备。由于该方案进行了深台面刻蚀(深度超过8 μm),因此需要一种评估方式来验证经刻蚀工艺后材料是否发生了反型损伤。图1为刻蚀工艺及后续器件制备的流程图。
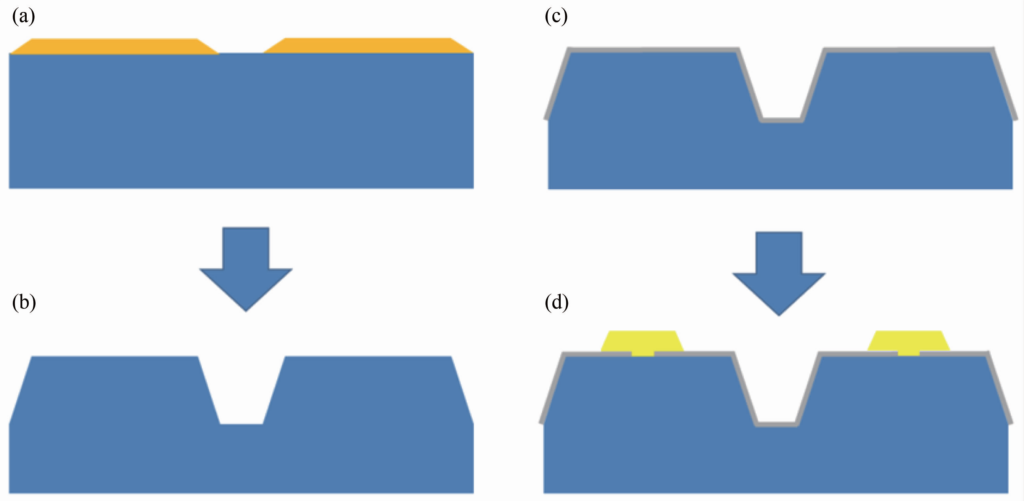
器件表征
在同一片Ⅱ类超晶格材料的对称位置上制备两个相同的电极(见图2(a)的上半区域),然后测试两者之间的I-V及阻抗特性曲线(结果见图2(b))。图2中,蓝色曲线为I-V特性曲线,红色曲线为阻抗曲线。由于电极与材料之间的功函数不匹配,存在肖特基势垒,所以I-V特性曲线为典型的肖特基接触的特征曲线。由阻抗特性曲线可知,左右势垒对称,因此两侧电极下的材料为均匀一致的材料,属于同种状态的半导体。随后将左侧一半的材料与材料表面的电极一起用光刻胶遮住,并将右侧电极用湿化学处理的方式漂掉。然后对材料的右半部分进行干法刻蚀。刻蚀后重新在右侧生长与左侧对称的新电极,并重新测试两侧电极之间的I-V及阻抗特性曲线(结果见图2(c))。可以看出,与刻蚀之前相比,该曲线特征没有明显的变化,说明现有的刻蚀技术没有使Ⅱ类超晶格材料出现反型。
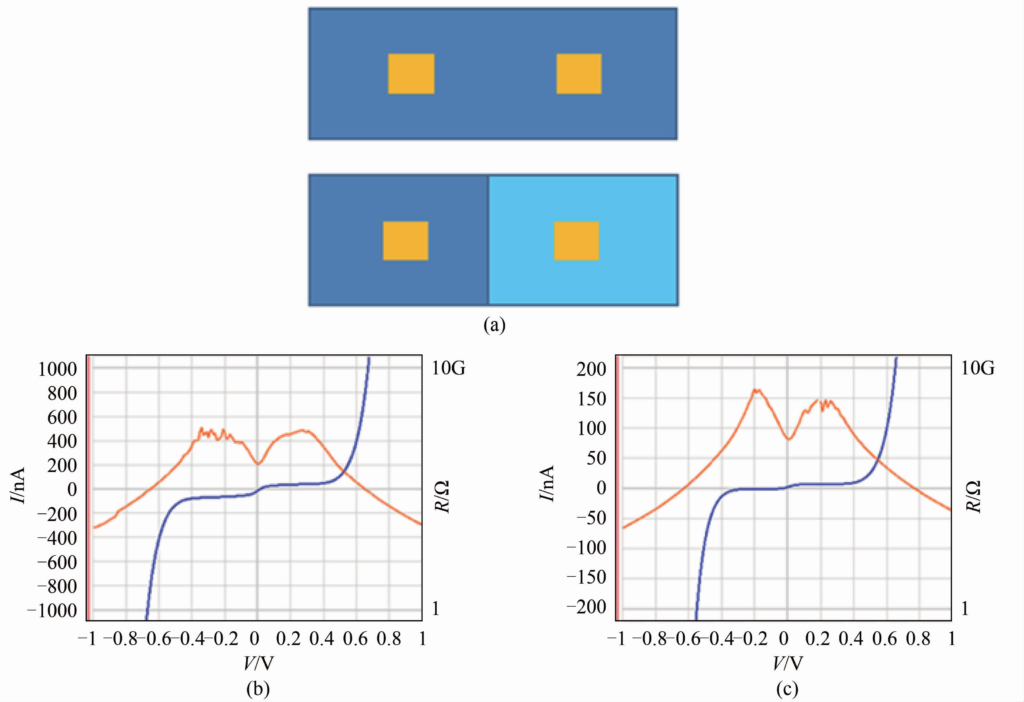
本文选用光刻胶作为干法刻蚀的硬掩膜。由于光刻胶的边缘有倾角,而且不同厚度光刻胶的倾角不同,因此将不同厚度的光刻胶作为硬掩膜,刻蚀相同深度的材料时,产生的深台面形貌会有所差异。我们可采用所制备探测器光敏面的占空比来衡量其具体差异。台面间距为20 μm。刻蚀8 μm深度后,擦去表面的光刻胶并进行形貌表征。采用的仪器为激光共聚焦显微镜。如图3(a)~图3(c)所示,光刻胶不断加厚,且将较厚光刻胶作为掩膜时刻蚀的台面会使器件有较高的占空比,同时也能有效隔离像元。由于深度测试的方式是在刻蚀后的芯片表面上直接用蘸有丙酮的棉签擦拭,所以会有少量残胶残留在结构的台面缝隙中,但台面整体的形貌并不受残留光刻胶的影响。因此,该方法不影响对刻蚀形貌的判断。
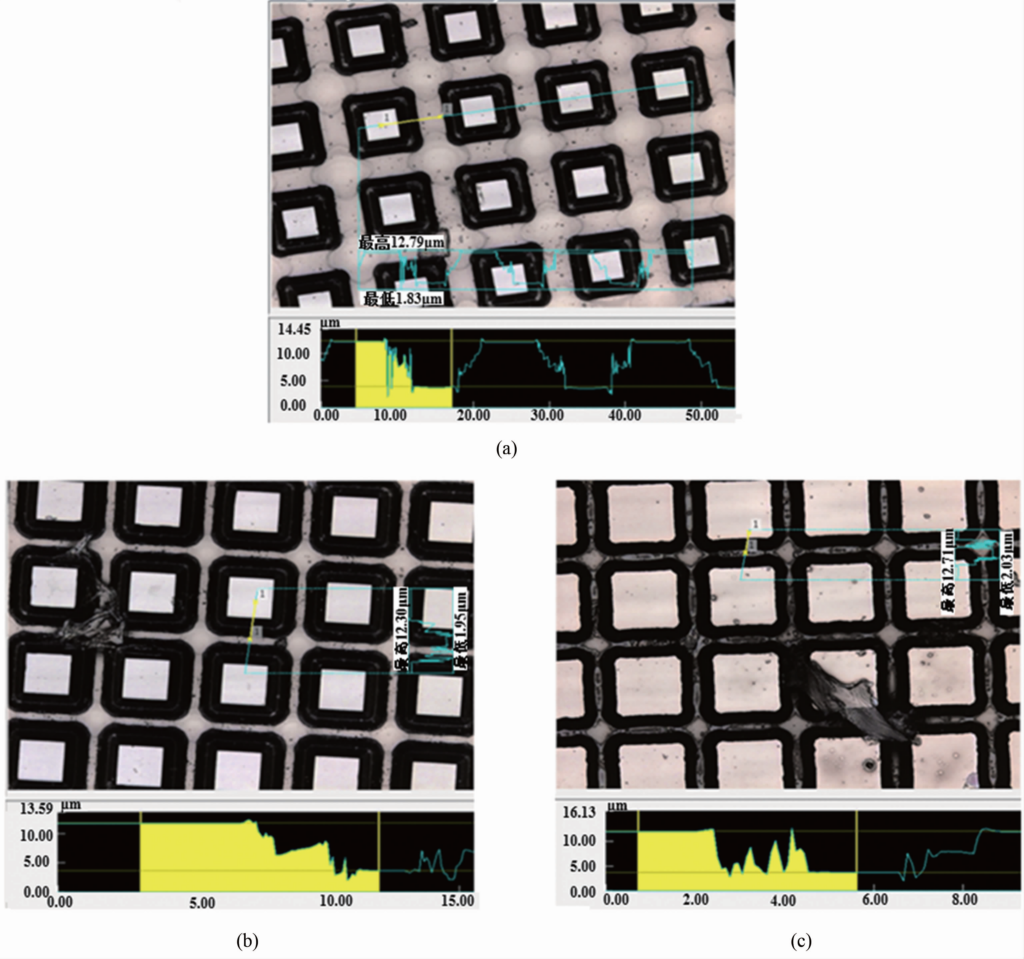
在确定最佳的刻蚀掩膜厚度后,为了获得良好形貌的台面,还需控制孔底生成物的生成,并在保证台面足够大的同时有效分离像元。于是采用变功率刻蚀的策略对Ⅱ类超晶格深台面进行刻蚀。主要改变对刻蚀形貌影响较大的射频(RF)功率,因其大小会影响刻蚀能量的强弱。固定刻蚀8 μm左右,其中前4 μm为刻蚀的第一步,后4 μm为刻蚀的第二步。
如图4所示,总共采用三种分步刻蚀的方式。如图4(a)所示,刻蚀前4 μm深度时采用较小的RF功率,后4 μm深度时采用较大的RF功率;如图4(b)所示,刻蚀前4 μm深度时采用较大的RF功率,后4 μm深度时采用较小的RF功率;如图4(c)所示,刻蚀前4 μm深度时采用较大的RF功率,后4 μm深度时采用较大的RF功率。可以看出,前4 μm采用不同的RF功率刻蚀后,台面面积并没有明显变化,而台面到底的斜坡宽度有一定的差异。采用较小的RF功率时,台面斜坡水平方向的宽度为1.6 μm;而采用较大的RF功率时,台面斜坡水平方向的宽度分别为0.9 μm和0.7 μm后4 μm刻蚀后,图4(a)中台面斜坡水平方向的宽度为1.8 μm,图4(b)中台面斜坡水平方向的宽度为1.8 μm,图4(c)中台面斜坡水平方向的宽度为1.2 μm。可见分步刻蚀中先采用较小的RF功率,还是先采用较大的RF功率,并不会影响斜坡宽度。全过程采用较大RF功率刻蚀形成的台面斜坡宽度只有1.2 μm。台面斜坡过于陡峭,不便进行电极钝化等工艺。而先采用较小RF功率、后采用较大RF功率的工艺,则可有效避免深台面刻蚀过程中生成物易于堆积的问题,同时还可规避台面过于陡峭进而影响其他工艺的问题。因此,在后续刻蚀中选择先采用较小RF功率、后采用较大RF功率的工艺。

在确定掩膜厚度及刻蚀工艺后,在正式工艺中进行低损伤、深台面的刻蚀。刻蚀形貌的不同放大倍数扫描电镜图谱如图5所示。可以看出,大规模焦平面阵列制备的台面形貌高度均一。大规模阵列中有效分离像元,台面底部较为光滑,侧壁没有明显的毛刺,台面没有产生生成物。现有工艺可以实现大面阵、深台面的刻蚀,为制备大面阵Ⅱ类超晶格焦平面探测器提供结构保障。刻蚀深度超过8 μm,缝隙深宽比可达2,实现了高深宽比刻蚀。
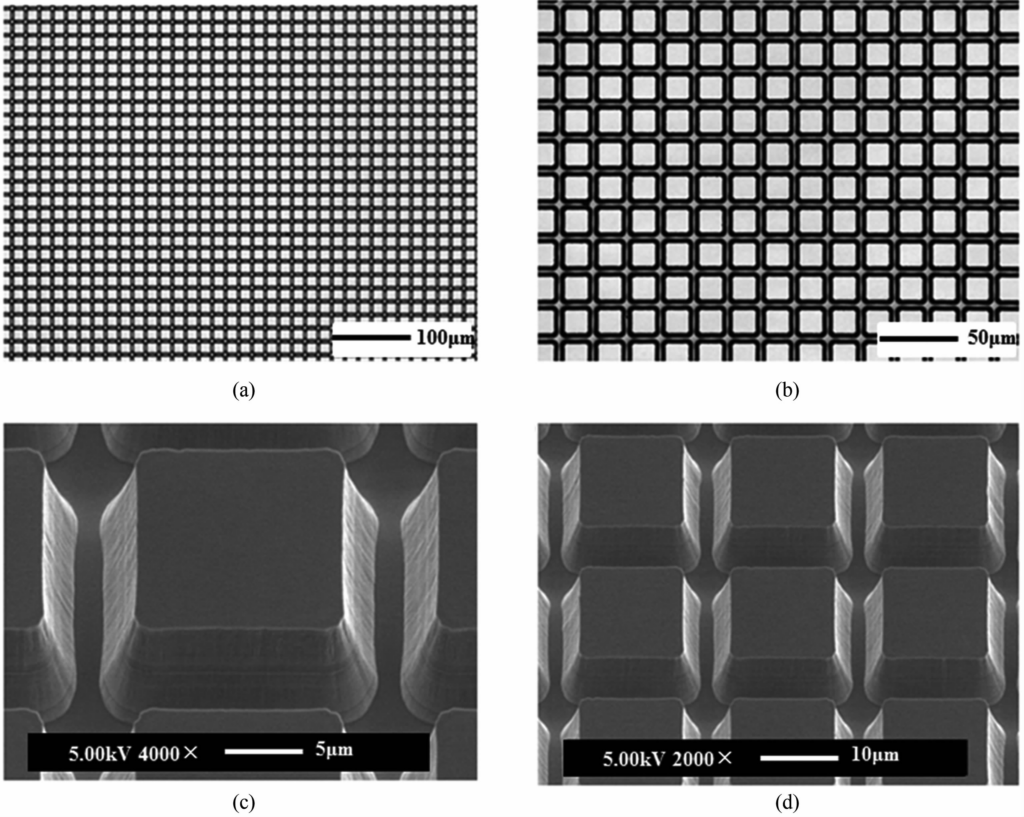
在中/长波双色焦平面探测器的制备过程中,刻蚀台面成型后,通过钝化和电极生长等获得焦平面器件。对器件进行了I-V及阻抗测试(结果见图6)。从图6中可看出明显的双阻抗特征,其为实现双色结构的两个背靠背np结。结合相关材料组分结构的设计判断,左侧明显的阻抗曲线为中波响应结的阻抗曲线,右侧尖锐的阻抗峰为长波响应结的阻抗峰;中波一侧的阻抗峰值为200 GΩ,平坦区超过1V。刻蚀损伤对探测器长波性能的影响通常更大(与中波相比)。测试曲线显示,该器件也具有明显的长波阻抗(峰值达100 MQ),且曲线中长波侧的平坦区超过100 mV。从电学角度可初步判断此探测器具有双色探测的能力。这进一步验证了低损伤、深台面刻蚀技术的可靠性。
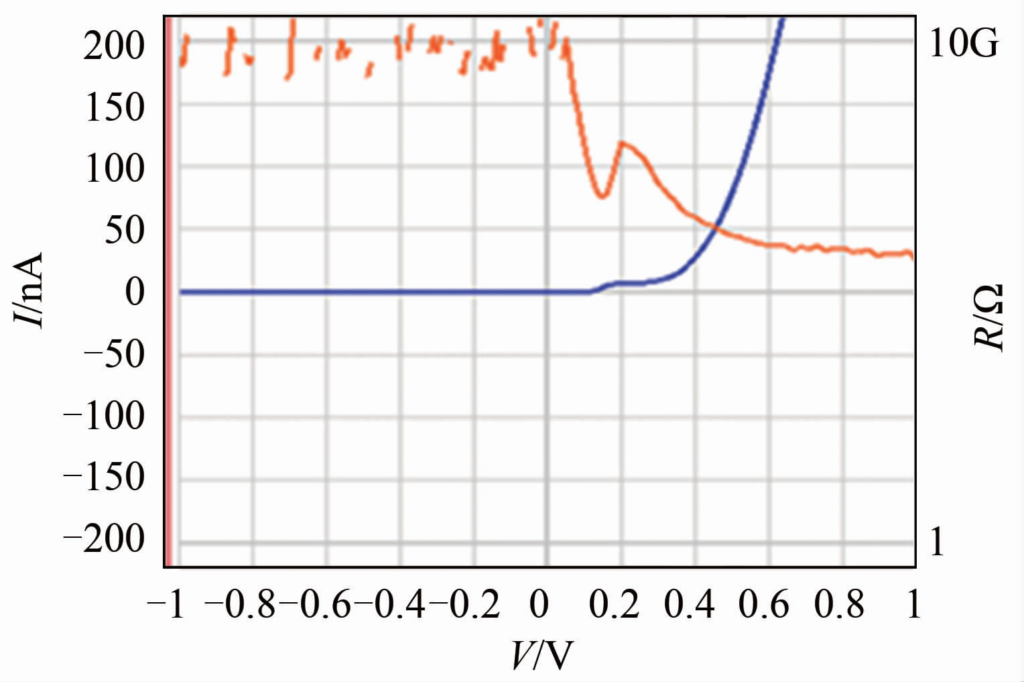
结论
本文采用对称电极I-V测试的评判方式,实现了对刻蚀是否发生反型及高损伤的判断。然后通过优化光刻胶厚度和采用分步变功率刻蚀工艺,实现了低损伤、深台面的11类超晶格刻蚀。相比于传统的一步刻蚀,该方法有效避免了生成物堆积以及侧壁过于陡直等工艺问题,得到了具有双色特征的I-V及阻抗特性曲线。所制备器件的长波阻抗峰值达100 MΩ,并且曲线中长波侧的平坦区超过100 mV。这项技术为高质量大面阵双色Ⅱ类超晶格探测器的制备提供了一种新方法。目前该研究已应用于640 × 512元(20 μm)中/长波双色Ⅱ类超晶格红外探测器的制备。后续研究中,随着像元间距的缩小,需对掩膜的抗刻蚀性作进一步研究以保障刻蚀质量。
论文信息:
DOI: 10.3969/j.issn.1672-8785.2023.03.001